By Kelly Bobki, GIS Supervisor, Water Engineering, and Phillip Brown, PE, MSCE, Civil Engineer
The Kansas City Board of Public Utilities (BPU) provides safe, dependable water and electric services across Kansas City, Kansas. As a nonprofit public utility, we are fully committed to serving our customers and the community as a whole. It’s more than simply providing a service. It’s a commitment to a better quality of life. The Water Department provides water to 55,000 customers. The water system includes 6,700 fire hydrants; 13,000 water valves; and over 963 miles of water pipe.
Legacy Solutions and Paper-based Workflows
Our legacy system contained tiled maps in AutoCAD drawing format, which contained a geographic information system (GIS) database on the back end. The tiled AutoCAD drawings split at the centerline of a road, and there were over 600 drawing files. We had a disconnected system. Finding assets in the field was a challenge for the field crews. Work management consisted of providing field crews with a sheet of paper listing an address or assets and what was to be done to the assets. The papers would sit on someone’s desk, or get lost in routing, and some never made it to the office from the field. BPU needed a better system for tracking and managing data.
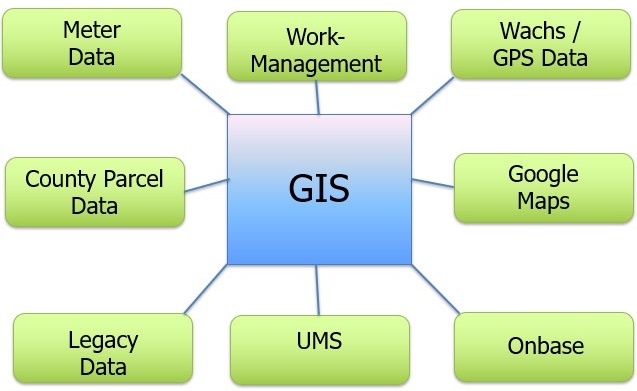
Modernizing and Making Data Accessible
We spoke with several vendors throughout our selection process and visited others at trade shows and conferences to help determine which would be best for our Water Engineering Department. Engineers in the department had used Esri in the past at different jobs, and after seeing some demonstrations, we decided this would be the best fit.
BPU implemented Esri’s ArcGIS and created an internal GIS site for all departments to access. ArcGIS enabled us to store all data in one location and pull in legacy data from older systems. We now had all data at our fingertips, displayed on useful maps.
During our GIS conversion, we also wanted to give our crews the ability to access and update the data in the field so we would no longer have to rely on paper.
Internally, we created our GIS websites using Geocortex and ArcGIS Online. We started with our field work order map and concentrated on our distribution system first. Since our GIS conversion six years ago, we now have all water departments accessing GIS sites. These include the following:
- Tap & Permit Maps—Used by our tap trucks and follow a service from installation to turning on
- Trouble Map—Used by our trouble service crews to complete customer service orders
- Backflow Map—Tracks backflow devices
- Valve Inspection Map—Yearly inspection of valves
- Hydrant Inspection Map—Yearly inspection of hydrants
- Hydrant Flushing Map—Tracks hydrants that are being flushed
Our field crews access our external sites using ArcGIS Field Maps through a mobile device. This allows both internal and external updates to assets to be seen in real time.
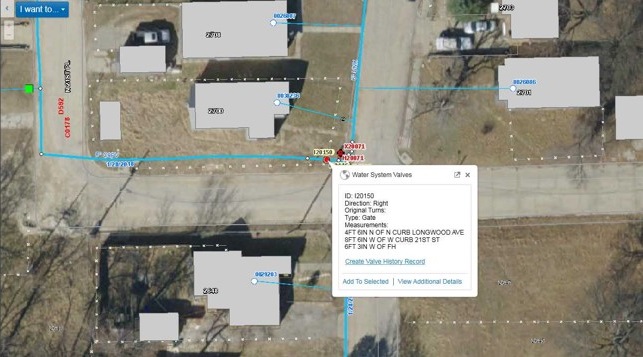
Improving Work Management
Our next focus was developing a work management system that would allow us to track our daily work; plan work in advance; track material used on jobs; and create workflows from start to finish on installation, abandonment, and maintenance of assets.
Using ArcGIS Online and Geocortex, we created a work management map. Work orders are created based on asset type (hydrant, valve, main, service) and given a priority of 1–5 that follows our business processes.
We also linked our locate data to this map. We set up script files to run on the back end to let us know when jobs were ready to work. When the red locate box appears on the map, this lets us know that locates are completed and the job is ready to be worked.
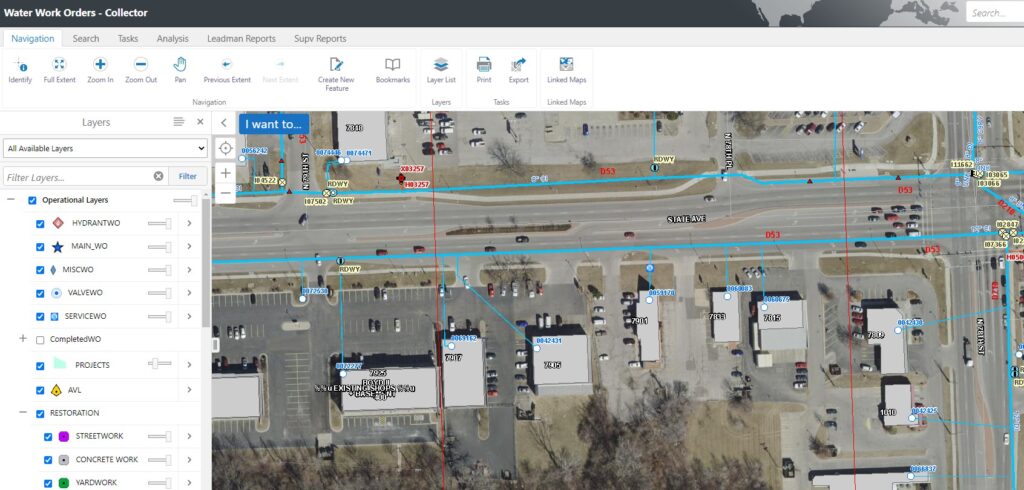
Using the ArcGIS Field Maps app, field staff can access work orders on their handheld devices and input the work they perform. This includes the material used, asset type, size, and manufacturer, and it also tracks start and finish times. We worked with our water leads to develop and implement this process. This increased the buy-in from staff and helped to ensure that the new solution would be used.
Field Maps has been an extremely useful and innovative tool for us to use. Between the pictures we upload to track the jobs and the attribute data on our assets, it has made record-keeping of what’s in the field very convenient and easy to access.
As water assets are installed, our engineer aides use survey-grade Carlson BRx7 GPS equipment to collect high-accuracy location information. Approximately 90 percent of our assets have high-accuracy locations stored in the GIS. This is a benefit to our water leads, because they can use Field Maps on mobile devices to get to the asset. They also have the ability in the field to view work orders that have been completed.
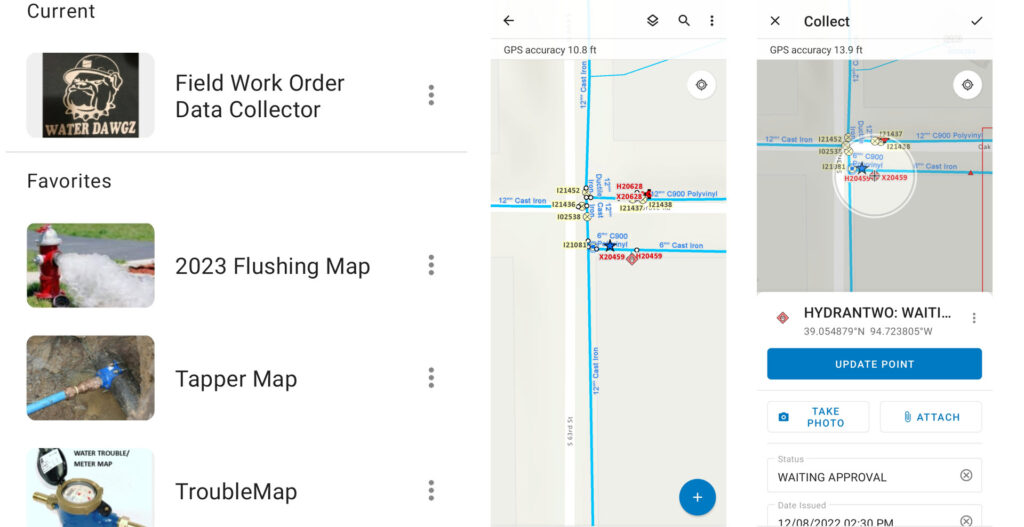
Follow-up work is captured on the work order using a restoration feature layer. This feature layer includes the size and type of the area that needs to be repaired. Once the water service lead completes the work order in the field, the status changes to Installed. Supervisors review the work and change it to Waiting Mapping. The assets and attributes are then added in the GIS.
The GIS has helped me immensely in my daily work activity. Whether that is using the GIS to help with new design or accessing older records for assisting crews with maintenance, the GIS is a one-stop shop that makes my job much simpler. It also helps that the GIS team is very active with updates and helping to train staff on using the GIS so that we are working with the most up-to-date information and using the GIS in the most efficient way.
ArcGIS Dashboards have been configured for our executive managers and distribution managers based on information that they request to see. The dashboards help to track our assets and monitor work order progress.
Working in a water system, our supervisors are always being pulled in different directions. Using ArcGIS Dashboards allows our management team the tools they need to visualize the current workload and better utilize our employees in the field.
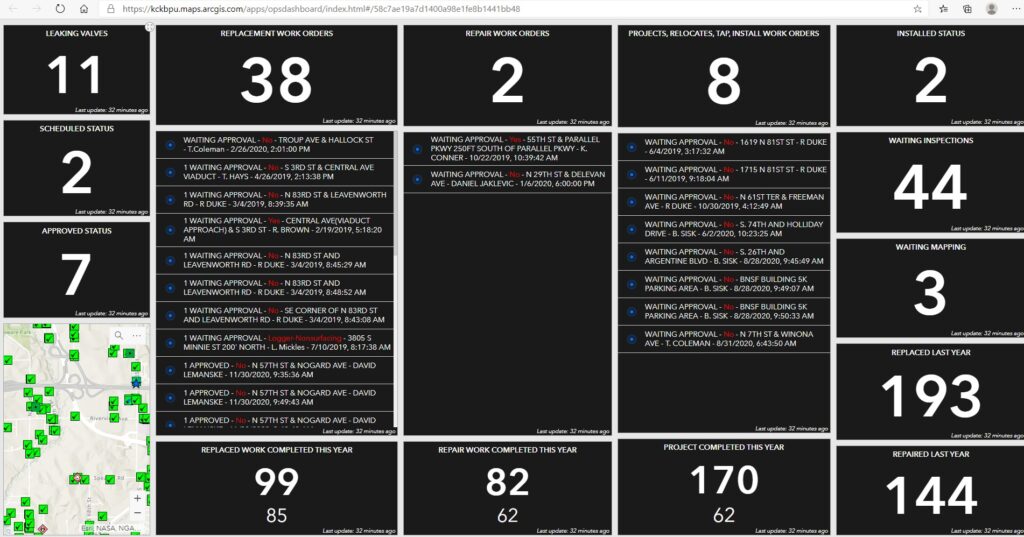
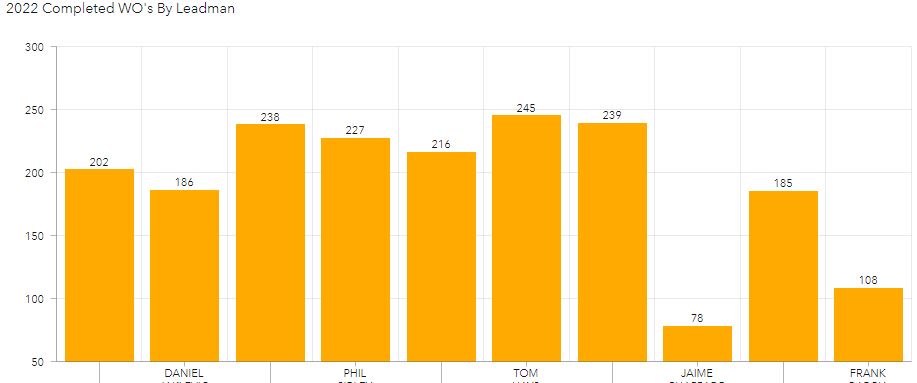
Converting from CAD to GIS Increases Efficiency and Cost Savings
The benefits of using ArcGIS products are plentiful. We now have one seamless map that contains all of our assets with all the associated attributes. Our field crews have access to live data in the field and can instantly see updates.
We are able to plan work ahead of time and give our customers notice on planned maintenance work and emergency work. We use Esri and Geocortex to display our water network; it’s as simple as drawing a polygon around the area of work to trace the shutoff; then, we export a file to our interactive voice response (IVR) calling system that places the call and text and lets our customers know we have a planned outage in their area. Our crews used to have to knock on doors and leave notices of water shutoffs.
Our crews are no longer going to a job and having to wait for locates. The locate data is displayed on the work order map and allows us to see if the locates are complete before we send the crew out to a jobsite. We are all familiar with the phrase “Time is money.” GIS has allowed us to be productive with our time and to focus more on achieving our annual goals.
Work orders are mapped within a day of installation. With our old process, it would have taken a couple of weeks to get paper copies back to the GIS department.
We have greater accuracy by adding pictures of our jobsites to the work orders before the job starts, during repair/replacement, and after the work is completed. Our liabilities have also decreased because the photos are the best protection from false claims of property damage.
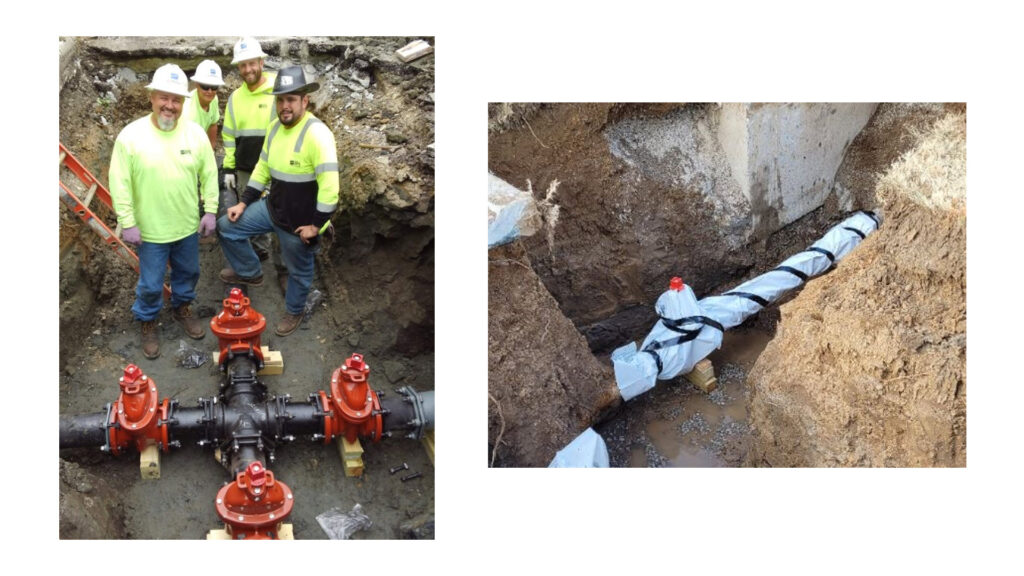
Our water service leads take pictures of the installations before the start of locates, during installation, and when the job is complete. This has saved the utility money in terms of claims: if we have a complaint from a customer about how a jobsite was left, the photos of the completed job help us in fighting untrue claims against the utility.
Below are pictures of a main leak; our crews capture the locates before digging, the exposed pipe, the repair made, and a final picture of the jobsite when the job is complete. All of these details are attached to the work order, including measurements, material, time, and photos, along with any follow-up work that needs to take place.
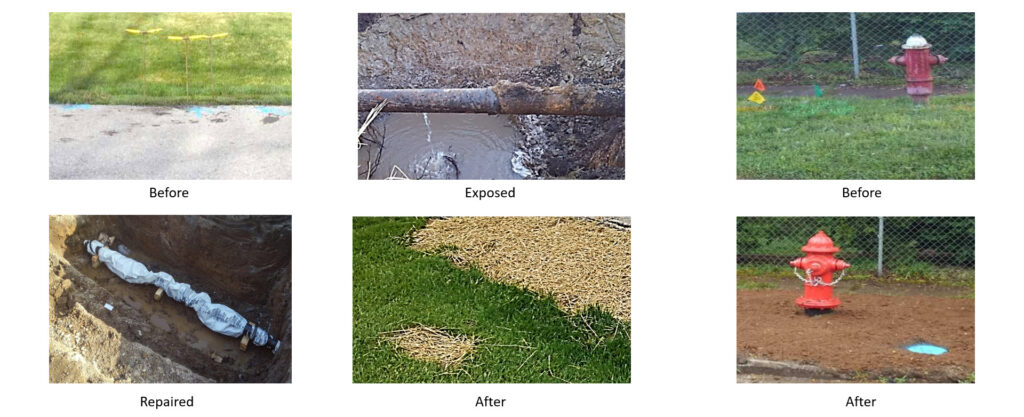
We continue to build and grow our GIS system to benefit all groups in the Water Division at BPU. We have created an asset management and work order system that benefits all users and allows us to easily extract data for reporting and statistics and to manage our infrastructure more efficiently and effectively.
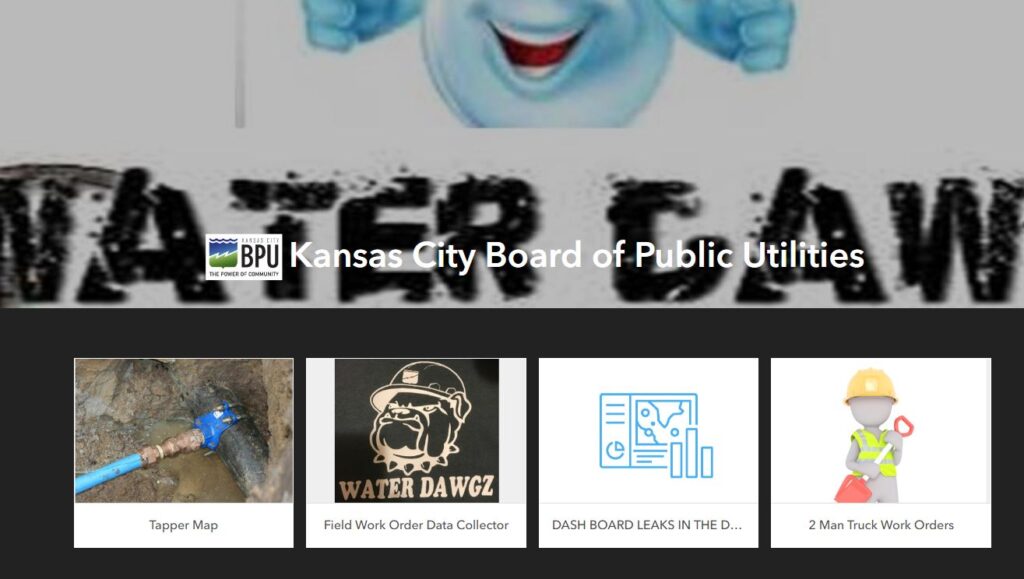
Esri has provided our engineering staff greater flexibility in designing projects, implementing and tracking work orders, and providing on-time asset management of our water system. The ability to analyze the performance of our aging infrastructure with Esri software is critical to prioritizing main replacements with limited funding available.
Stay Connected with Esri’s Water Team
ArcGIS is an extensive information system that enables modernization of workflows with easy-to-use applications for the field and office. Strengthen your organization with smart water solutions that will increase efficiency and provide insight for decision-makers. Visit the Esri Water Utilities web site for more information.
Join the Water Utilities Community
Follow #EsriWater on social media: Twitter | LinkedIn
Subscribe to the Water Industry newsletter “Esri News for Water Utilities and Water Resources“
Learn more about how Esri supports Planning and Engineering.