In the past five months, Covid-19 disruption has been a wake-up call for supply chain, and it accelerated a few trends in the industry. These trends can be digitizing the supplier and distribution network to visualize dependencies across the network globally, adding risk layers and potential restrictions and development of maps and dashboards to share the results with stakeholders.
As my colleague, Frits Van der Schaaf, presented at UC 2020, to build this “Digital Twin” for the supply and distribution network we developed a five-step process, serving as a foundation for this process:
- Step 1: Organize and map your location data. Geocode supplier and
customer locations. Create territories, perhaps based on ZIP code or
drive time. - Step 2: associate metrics with the location such as orders, products,
flow of materials and data that resides in CRM systems, spreadsheets
etc. - Step 3: Visualize and monitor supply dependencies, for example, with
near real time data and decide on regional changes in inventory level
based on anticipated demand. - Step 4: Use all the data to perform spatial analysis to assess risks,
understand where there are new markets for instance, requiring a new
distribution center. - Step 5: Share results from analysis that can be communicated through
maps and dashboards.
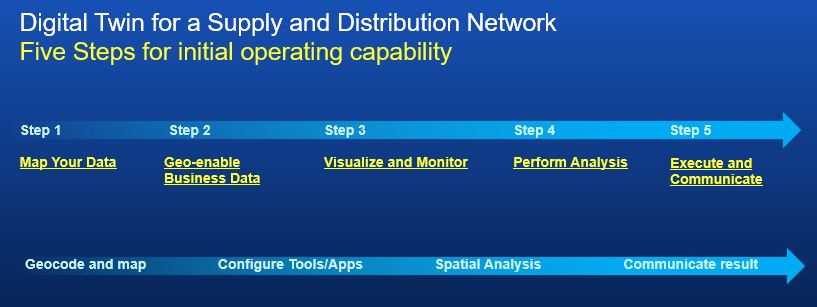
With such foundation in place, the goal would be to ultimately build a digital twin of the supply network that has a way to maintain open communication with the physical network. The digital twin will help decision makers to make accurate and timely decisions digitally and apply it to the physical network with greater efficiency.
In this regard, data is always going to be an issue to pay attention to. Data accuracy needs to be a part of all metrics we develop for the system, and we need to have ongoing training opportunities for everyone working with the data. The United Parcel Service (UPS) is a great example of successfully developing and deploying an innovative technology to package flow. As stated by Jack Levis at the Esri User Conference Supply Chain and Logistics SIG 2020, Twenty years ago, when they started this effort, ORION was only a data infrastructure to change how UPS operated and then it evolved over time by bringing advanced optimization and geospatial data into it. The goals for UPS developing ORION were saving time, reducing costs, improving service and creating an infrastructure to add new service products. They needed to transform the information into data models. Therefore, they started with analysis of data in the first step. Then, with utilizing the geospatial technology and visualizing the data on the map, they helped the frontline supervisors to make smarter and faster decisions where every package sent (to hear the whole story, click here).
As digital transformation continues to accelerate, business executives face many major responsibilities and new challenges across the supply chain. By adopting the right technology tools and metrics to handle the large amount of organizational data, businesses can run more efficiently, mitigate risk, and ultimately offer a better customer experience.