This blog aims to identify 5 ways in which railroads can make use of their existing tools and data to improve safety and efficiency and reduce cost. Many railroads have successfully implemented GIS tools and databases to manage things like their real estate and physical rail assets. Under the Valuation Act of 1913, the Interstate Commerce Commission used maps to assess the value of every railroad in America. Many of these valuation maps or “Val Maps” can still be seen today in vaults and map rooms in railroad offices across the US. These maps were eventually digitized and are the origins of GIS as we know it today. 100 years later, Positive Train Control (PTC) is implemented, and the railroads are required to map their physical assets more accurately than they ever have before. This further enhances their GIS and opens up endless possibilities to utilize this new information in ways never before possible. Let’s take a look at some of those ways.
HiRails trucks travel along the rails as well as in and around rail yards. During my time at a Class 1 Railroad, I was approached by a member of our tax department. As with most of the new business partners who approached me, she simply came to me with a problem and didn’t really know how, or even if, GIS could solve her problem. She had been going over our fuel spend for the entire network and one item had caught her attention. We purchased a lot of fuel in many of the 22 states we operated in and were paying the states fuel surcharges in each. The fuel surcharges are then used to repair and replace the roads that are used while the fuel is being consumed. The problem was, we weren’t operating on roadways with much of our equipment. It stayed inside the confines of our rail yards or along the track. Could we prove to the states, with data to back it up, that we were eligible for a past refund and reduction in tax going forward? We had been tracking our vehicles for years, so we were able to compile several years of vehicle GPS data. We had data for our track network and real estate layers around our yards. The analysis we performed was exactly what makes GIS and spatial analytics so powerful. We were able to plot every single GPS ping from each of the vehicles we had been tracking against all of our private property and assign a value of on property or off. We were then able to create a wide variety of reports defined by time on and off property, number of vehicles on or off property, length of stay on property, etc. With all of these metrics now complete and visually represented in dynamic maps, we presented our findings to the first state. They were impressed and agreed to wave a portion of the last three years of fuel surcharges and to lower our future tax liability by the percentages we demonstrated. This process was then repeated for each of the states we operated in and I cannot recall any state having an issue with our findings, all agreed to some form of tax relief based on our analysis.
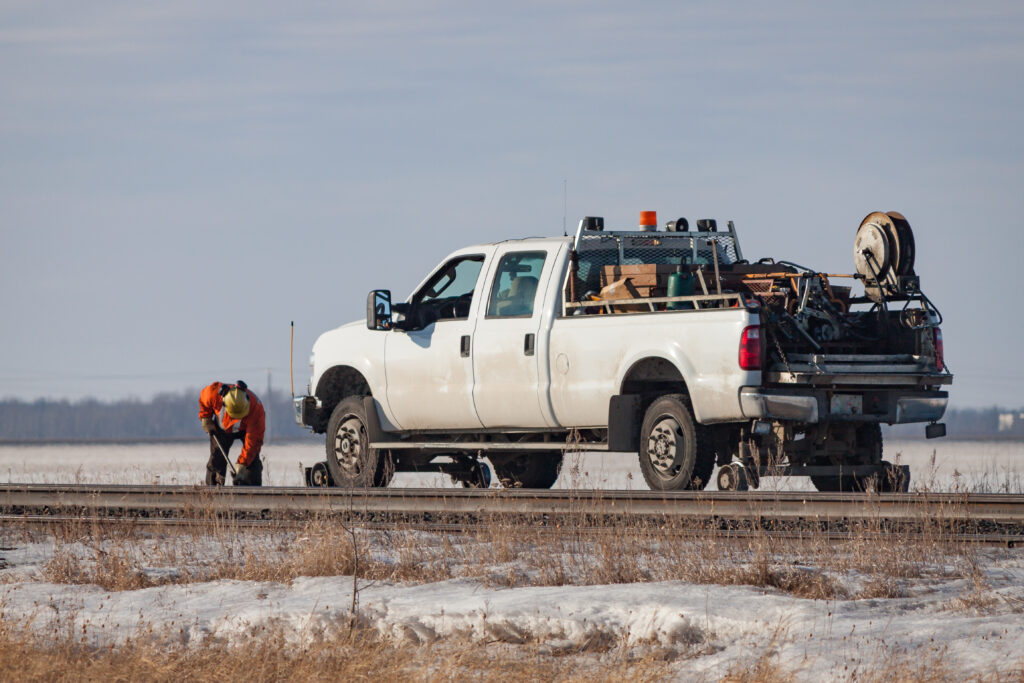
Railroads certainly have no shortage of data. They record everything from locomotive GPS pings to freight car movements and their deliveries at customer locations. They have records for track installations, inspections, maintenance and even the tonnage of freight over each piece of track. One of my favorite things to do with GIS is to provide a new angle or aspect to the same data railroaders have been looking at for decades. In this case, I had a business partner come to me who was new to the railroad. She was a recent graduate in Mathematics and wanted to better understand our data to see if she could create an algorithm to define the amount of time we spent serving each of our customers. She was interested in looking for trends and anomalies in the data that the operations team could then focus on to improve deliveries. She asked many interesting questions about how trains set out and picked up cars at facilities, whether the engines were operating forward or backing and if we could determine that from the data, what exactly were mileposts and why were they not all one mile apart. These were all critical questions to her understanding what the data meant. We focused on a few customer sites that provided a variety of layouts. I was able to replay for her the last few weeks and months’ worth of movements simply by using the ArcGIS Desktop Playback Manager since the ping data had fully accurate time stamps. What this process did was allow her to visually see exactly what those otherwise cryptic GPS pings meant in real life. As I scrolled through different days, different trains, and different customer facilities, I could see her eyes light up and the wheels turning as she was forming her hypothesis. She was learning how to interact with this data now that she understood the exact correlation between the customer IDs in the train consist, the train crews reporting of what they had done on site, and the GPS pings defining exactly what the engines did. She stated several times that she never would have been able to fully understand that correlation if she could not visualize it. GIS gave her that visual correlation. The project was a success and went on to identify ideal times we should be striving for to serve our customers. It identified many problem areas where we did not have a good plan in place or the right crews to serve complex facilities and drove operational changes to improve efficiency.
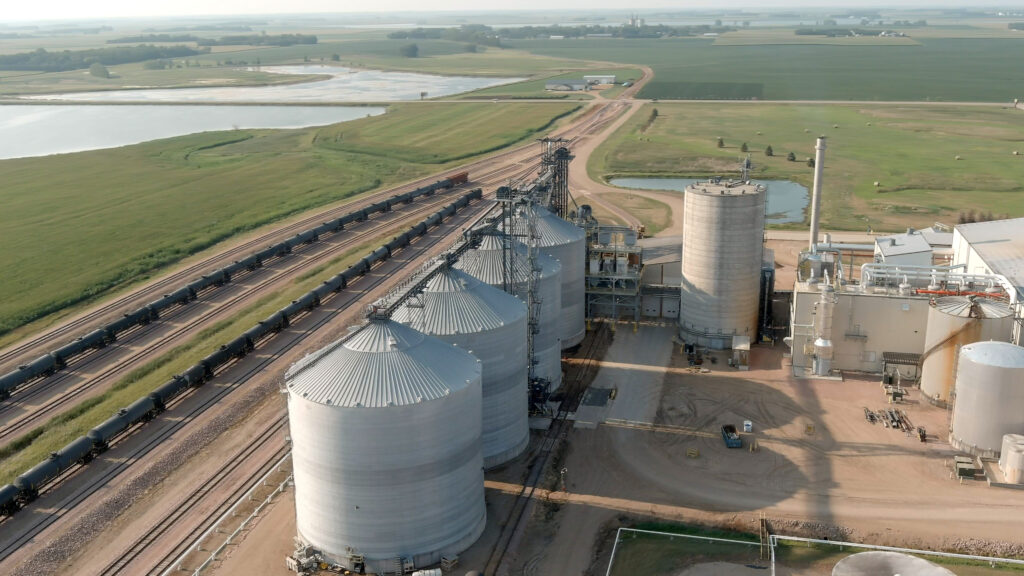
Emergencies like natural disasters are inevitable. Companies need the flexibility to respond to a wide variety of situations with the right technology. Portal for ArcGIS is incredibly flexible and allows for rapid deployment and modification to fit the situation. In 2018, Hurricane Florence was headed towards the North Carolina coast. I oversaw a team of field managers who all had drones and could be in the area after the storm passed to conduct damage assessments. What we needed was a way for the teams to take lots of photographs on the ground, as well as in the air, and present them back to a team in a command center in Florida. With only a few days to prepare, Portal was chosen, and our GIS team stood up a mobile application for the field teams and a web application for display and interaction in the command center. The decision was made on a Monday to build the apps in preparation for a storm hitting on Friday night. The teams were able to build a basic observation data layer capable of recording a handful of observable attributes about the damage and the status of the railroad around it. The layer was published in both the web app and mobile app and deployed to the field mid-week. The storm hit Friday night, and the teams met up with maintenance crews Saturday morning to begin the damage assessments along the track. Traditionally, a conference line was opened for crews to call in and report verbal damage assessments to the executives in Jacksonville who would try to match the reports up with assets in the area. With the new app in use, the team at headquarters was immediately seeing reports coming in on top of assets with conditions, power reports and photographs of the areas. The damage from Florence was quite severe so this reporting went on for days while the teams continued the clean-up. At first, we thought all the benefit would be for HQ decision makers to get real-time, accurate reporting. We quickly realized the teams in the field were getting great benefit from having the drones in the air to see beyond the immediate damage they were working on. They loved the damage assessments that were attached to each asset, so they had a log of exactly what work needed to be done. As for the team in the command center, there was great benefit in having access to the living atlas to add things like weather and flood gauge data. They requested several other rail assets be added into the map so they could assess the possibility of damage due to the impending flooding. Portal proved to be the right tool for the job that week and it demonstrated the power of having fast, accurate spatial information.
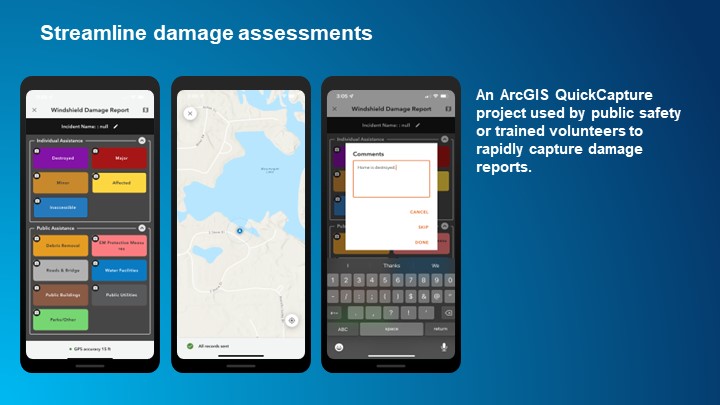
Not long after the successful launch of the damage assessment tool during Hurricane Florence in 2018, Hurricane Michael formed, and we were back to work. One of the issues a railroad faces in a high wind event like a hurricane is the need to “Tie up” all of their road crossing gates so the wind does not snap them off. This can only be done once it has been determined there will not be any more trains running in an area since you will not be protecting crossings anymore with the gates up. There are a lot of factors that go into this process since you need to take the path of the storm into consideration, where to stop trains in a safe location, which crossings to close and then how to assign the physical tasks to all of the responding field workers. Once the storm has passed, more decisions need to be made to return and untie the gates so train traffic may resume. All these decisions involve spatial analytics, and visualizing the data is critical, making GIS the perfect tool. We had added live storm models from the living atlas and the road crossings to our damage assessment tool. The tool also had a live view of the locomotive traffic in the area and where dispatch had halted train movements. All of this information in one place allowed signal teams to easily identify all the crossings they wanted to tie up. We quickly created a status field that allowed them to toggle between the stages like: needs tie up, tied up, needs to be untied, cleared, and damaged. These crossings spanned many miles in South Florida so it was incredibly valuable to be able to show these statuses on a color-coded map as well as in a dashboard so the decision makers handling the recovery could instantly see how many were tied, needed reopen and were cleared for trains. When storms hit, the railroads have their hands full with preparation before, protection during and recovery after and having a powerful tool to help provide them clear and concise actionable data is paramount to a quick return to service.
This next story talks about the struggle GIS departments go through to find sustainable funding to do what they do best. Positive Train Control (PTC) was an unfunded government mandate that required railroads to create a basemap of their network to an extremely accurate level they had never done before. We knew where our stuff was, but not to survey grade accuracy over 20 thousand plus miles. We certainly weren’t surveying and playing it into the data before the next train rolled by when things changed. I was faced with building out a team of field survey managers who could cover 20,000 miles of track and watch hundreds of teams who could potentially make PTC level changes to track assets every day. These could range anywhere from large scale siding extensions or double tracking, down to the widening of a road crossing by adding just a little bit of leftover asphalt after a repaving job was complete. Both projects, by PTC definition, had to be surveyed and updated in the Subdiv files. Again, this team was brand new, and the assignment was new. I was asked to come up with an annual budget. At first, I looked at the overall cost of my teams functioning on a 12-month basis and came up with a total cost of operation. Initially, this was thought to be an operating expense item, but I thought differently. If we were required to respond to all of the capital improvements completed, by federal mandate, why couldn’t this be included in the capital costs. I went before the capital committee, and they agreed the function should be included as a capital cost. This was good news, but it did not mean funds were allocated. When I took that to the operations teams who had the funding for track maintenance, I was told that 7 figure level of funding was not in the budget. I talked to the team that handled project management to better understand how the individual projects were broken down by line items. Up to that point, we had been getting small amount of funding on each project for “PTC Survey”. I took the time to explain the process and requirement to have our surveyors out on every project in a timely manner. The finance teams now looked at the ask in a different way and were able to add a new line item on every single project. We were given that line item for the small amount it would take for just that project, but it was now inserted in every single project across the network. We were now authorized to spend on every project for survey and the total amount was far more than my original ask for an individual budget. Despite having been in the GIS industry for over 20 years, it is still a relatively new entity in a 200-year-old industry like rail. We need to continue to think creatively at how to insert the technology in a way it provides the best return on investment to the business.
Each of these examples were very specific to a business need or request. I shared each of these to raise awareness of the kind of out-of-the-box thinking it takes sometimes to sell and grow the reach of your GIS capabilities throughout your organization. Esri offers plenty of resources to help you get started sharing the wealth of capabilities. You can visit our ArcGIS Solutions pages to see free, ready-to-use templates to help you jump start your project. The Esri Rail Industry Pages help connect you to industry specific solutions, resources and other colleagues. You can also sign up here to be on our mailing list and get notified of the latest news/updates.