What could the COVID-19 pandemic do that a trade war and natural disasters couldn’t? It could drive a US manufacturing revival.
There’s a renewed mandate for businesses to minimize supply chain disruptions—and savvy company leaders are discovering that the same location technology they use to manage global logistics routes can now help revive manufacturing operations stateside.
Supply Chain Disruptions Drive Change
At the onset of the pandemic more than two years ago, experts warned of possible supply chain disruptions. Risk management adviser and insurer Willis Towers Watson urged companies to analyze their business relationships, mapping the paths between multiple tiers of suppliers to better understand where parts and services originated in order to minimize bottlenecks.
Those who didn’t study their supply chains and prepare fallback plans—and even some who did—have felt the sting of pandemic shortfalls. Nearly three-quarters of American manufacturers in a recent National Association of Manufacturers survey said supply chain challenges had negatively affected their outlook for production, hiring, and capital spending. Almost half said they experienced production disruptions of one week or greater during the final quarter of 2021, with many pointing to delays in component parts, labor shortages, or logistics challenges.
Now, according to recent reports, some companies are rethinking their manufacturing operations to minimize disruptions from border closures and virus outbreaks, increase predictability, and bring supply chains closer to their customers, despite high labor costs.
The New York Times recently highlighted technology firms that are now constructing semiconductors and memory chips domestically; a US apparel supplier making clothing with American-grown materials; and major car manufacturers erecting factories to build electric vehicle batteries nearer to car buyers.
A supply chain shift of such magnitude calls for a nuanced and precise view of a company’s connections and dependencies. Industry leaders have gleaned this level of location intelligence from a geographic information system, or GIS technology.
Where Risks, Incentives, and Labor Exist
As companies shift supply chains, they’ll turn to GIS to analyze important geographic questions: where raw materials are coming from or products are going, where extreme weather risks are emerging, and where available economic development incentives and skilled workers create an attractive business climate.
Location intelligence can help executives test what-if scenarios and avoid supply chain disruptions. A company considering a new factory, for example, can use GIS to model where suppliers are relative to the proposed site, and the lead time required for various parts and subassemblies. A supply chain executive can identify new suppliers or plan the strategy for a new distribution site, visualizing how many retailers it can reach, in what time frame, and at what cost.
Business leaders can even map and model supply chain strategies to better understand and avoid climate-related risks. Data analysis reveals whether a prospective supplier location or headquarters site may eventually be starved for operational resources such as water. Location data can also show whether a city is prone to flooding or excessive heat, which can impact business operations. As part of their financial planning, executives can map available state and local incentives, as well an area’s renewable energy sources, creating better spatial understanding of each location’s assets.
For companies considering reshoring, hiring a quality workforce will be critical. Workforce planners use GIS technology to visualize valuable information about local talent pools, even tapping census data to see the education levels in an area to determine where to target recruiting efforts.
As manufacturers consider new factories in the US to avoid supply chain disruptions and other overseas complications, they’ll need insight on key business priorities. Whether analyzing the locations of suppliers or customers, production facilities or distribution sites, talent pools or climate threats, leading executives will rely on location intelligence to better understand the risks and benefits of domestic supply chains.
The Esri Brief
Trending insights from WhereNext and other leading publicationsTrending articles
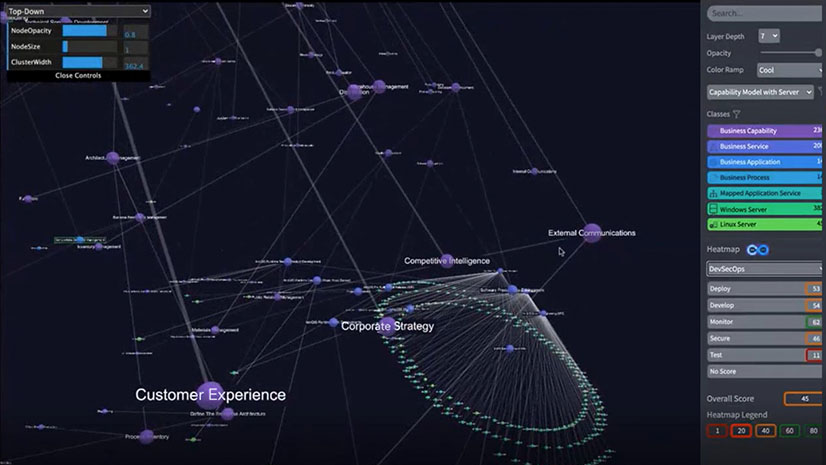
December 5, 2024 |
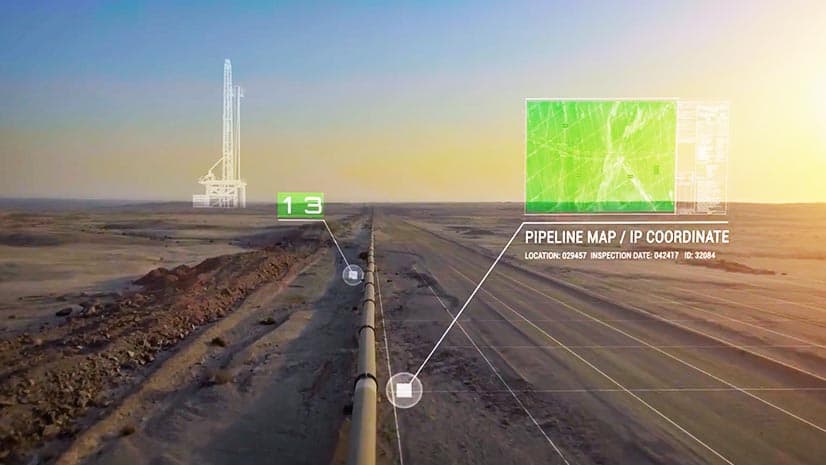
November 12, 2018 |
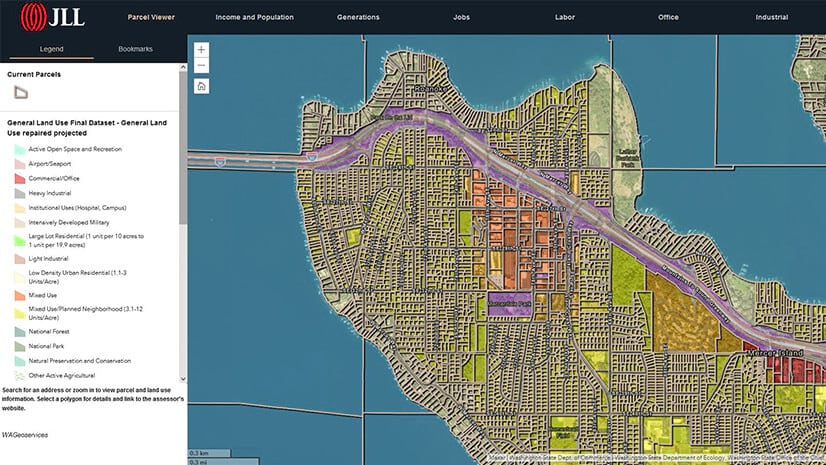
July 25, 2023 |

February 1, 2022 |
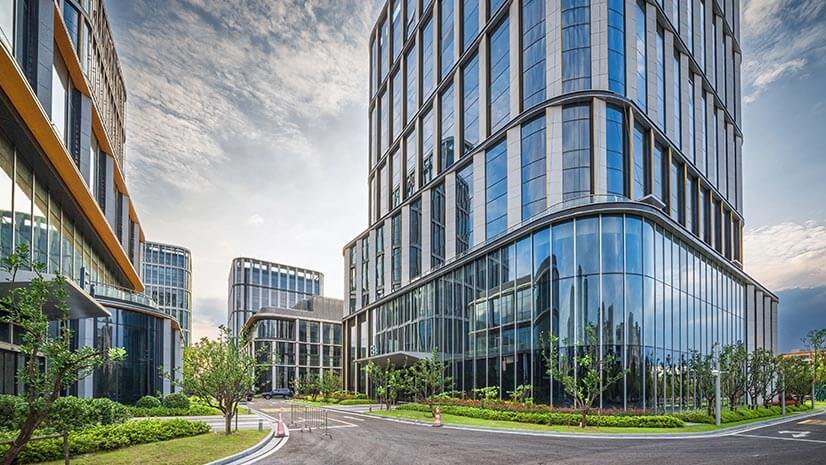
March 18, 2025 |

May 28, 2025 |