Last fall, California governor Gavin Newsom announced that all new cars sold in the state will be emission free by 2035. As the state with the most registered vehicles—twice as many as runner-up Texas—California’s policy will have a significant impact on the country’s transition to electric cars powered by lithium-ion batteries. Miners, manufacturers, and logistics companies stand to benefit if that policy sparks development of the state’s own lithium reserves.
If those industry players create a Southern California hub for lithium extraction and battery production—an outcome the state is encouraging—location intelligence will be key to making the process efficient and collaborative.
From Imperial Valley to Lithium Valley
Most lithium today comes from Australia; China; and the “lithium triangle” that covers parts of Argentina, Chile, and Bolivia. California’s Imperial Valley, a desert region in the southeast corner of the state, could contain even larger reserves.
According to a recent study by SRI International, highlighted in Bloomberg Businessweek, the magma-heated brine underneath the Salton Sea could annually yield eight times the amount of lithium produced globally in 2019. With the lithium-ion battery market on track to reach $129 billion by 2027—up from $37 billion in 2019—the Salton Sea’s lithium could be in high demand.
Geothermal plants already dot the shore of the inland sea, pumping the brine and converting it into turbine-powering steam. Several companies have expressed an interest in extracting lithium before the brine is sent back underground, according to Businessweek.
California officials hope manufacturers will build battery factories—and perhaps even plants that assemble electric cars—creating an industry cluster in a region officials have rebranded “lithium valley.”
A Unified Lithium Supply Chain
This kind of ecosystem could consolidate a key part of the electric car industry in one area, creating supply chain efficiencies for the companies involved and benefits for the local area as well as the state.
This will require cooperation among diverse stakeholders, beginning with energy companies, mining interests, local officials and community leaders, and environmental groups—potentially expanding to include battery and car manufacturers.
In other industries, such cooperation has started with a smart map of an area, stored and accessible with geographic information system (GIS) technology. Mining companies already routinely use GIS to create detailed maps of their sites, for everything from exploration to operations. Integrating satellite imagery, remotely sensed lidar data, and even point cloud maps created by drones, these companies gain a complete picture of a project. The data helps companies identify the location of deposits, strategize how to extract them, organize the daily operations of the site, and track the environmental impact of these activities.
For any cluster that might develop near the Salton Sea, a smart map could be a platform for communications among the various interests, with cloud-based permissions governing which companies and individuals can access which data. That kind of shared ground truth promotes transparency and can drive collaboration within industry coalitions.
Easing the Environmental Footprint of Lithium
One consistent criticism of electric cars as clean-energy solutions is that extracting and processing the key elements in lithium-ion batteries is itself a carbon-intensive process. Extracting lithium from brine involves large amounts of water, and both requires and produces chemicals that are potentially harmful to local air, water, and soil.
Some projects in South America’s lithium triangle have come under fire for misuse of local water reserves and for inattention to the environmental cost of lithium mining.
Location intelligence could help the companies pursuing Salton Sea projects maximize both efficiency and sustainability, similar to the way other resource-intensive companies are using location intelligence. For instance, GIS technology could monitor the yearlong lithium refinement process. As lithium production ramps up, the same system could help lithium-ion battery makers plan factory sites and manage the logistics of distribution.
Growing Lithium Valley
If the battery factories materialize, they’ll integrate locally produced lithium with other battery components sourced from around the world. Factory owners can use location intelligence to monitor their global supply chain and reduce the risk of disruption, as automaker GM has done for years.
Cobalt, another key component in electric vehicle (EV) batteries, comes from several countries that have been accused of exploiting mining labor. To ensure that they do not perpetuate bad labor practices, battery makers could follow the example of food and beverage companies that track the sources of palm oil to control deforestation.
Once the lithium in the batteries leaves Imperial Valley, a Salton Sea lithium industry could continue to exert a positive influence. Companies around the world are beginning to see their products as part of a circular economy rather than one that extends in a straight line from the manufacturer to the consumer to the landfill. When the Salton Sea lithium leaves the area in battery form to power electric cars around the world, manufacturers could take a location-intelligent approach to recycling. A manufacturer could estimate the life-span of any given battery, contact the owner around the time the battery is likely to expire, and offer buybacks. Instead of winding up in landfills, some components of the battery could be reused and reintegrated into the industrial process, creating a profitable and sustainable circular economy.
Building a lithium valley will take time, determination, and patience. But with a holistic application of location intelligence technology, an outpost of the world’s clean-energy future could bloom in California’s desert.
The Esri Brief
Trending insights from WhereNext and other leading publicationsTrending articles
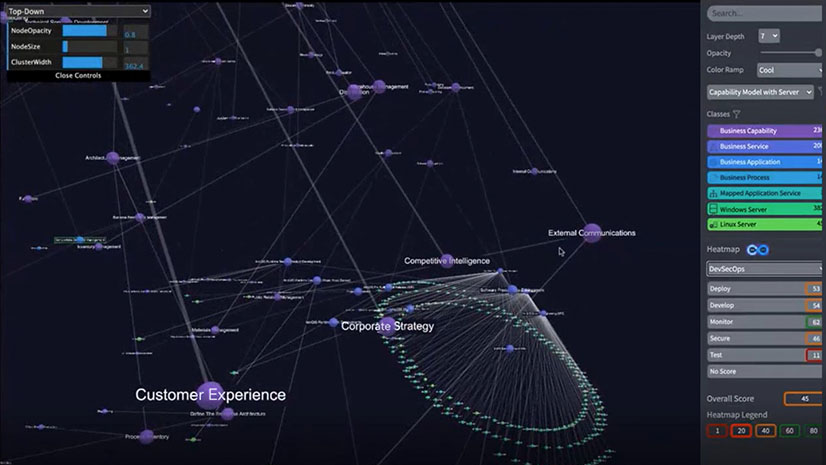
December 5, 2024 |
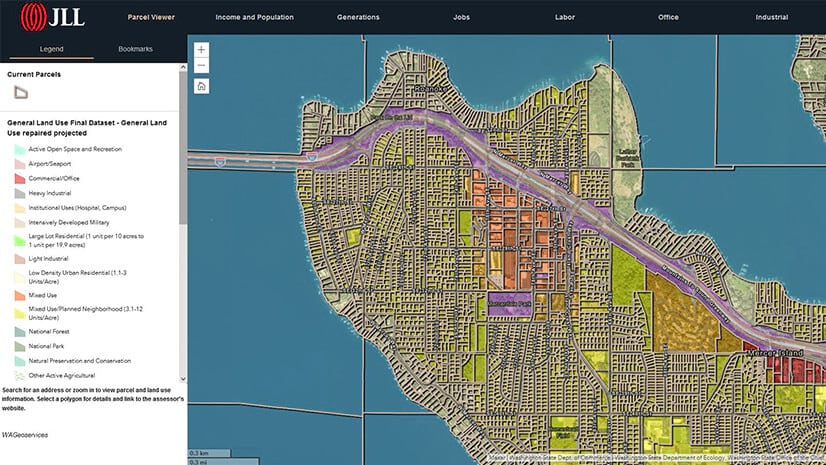
July 25, 2023 |
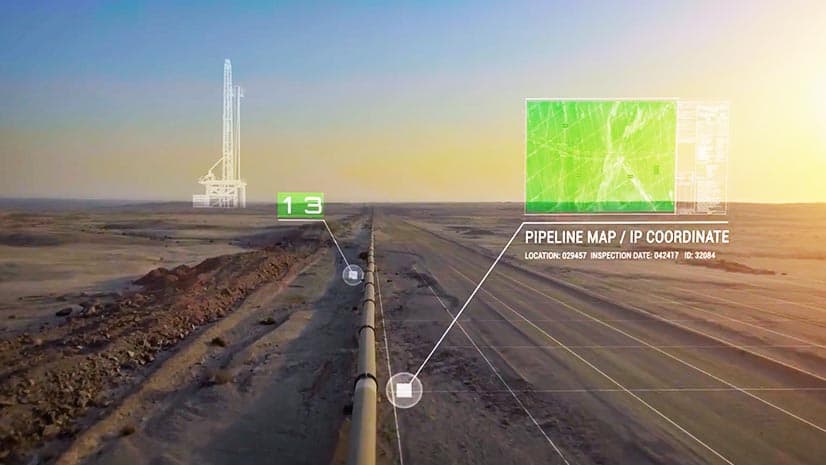
November 12, 2018 |

February 1, 2022 |

July 29, 2025 |

June 10, 2025 |