As stories of oceanic garbage patches and textile-laden landfills proliferate, reducing waste is becoming a business imperative for sustainability-minded executives. Leaders in construction—one of the biggest waste-producing industries—are creating greener waste management practices through a novel form of operational intelligence.
In the US alone, construction produces over 600 million tons of waste per year, debris that ranges from concrete to glass to wood, according to the Environmental Protection Agency. Minimizing what’s thrown away is an important sustainability practice. It’s also a criterion for securing certifications such as LEED, BREEAM, or B Corp, all of which require waste management plans.
Architecture, engineering, and construction (AEC) organizations committed to cutting waste will benefit from technologies that speed up data collection, improve reporting accuracy, and deliver operational intelligence. A geographic information system (GIS) reveals where certain types of waste are produced and where they should go next for minimal environmental impact.
Through a combination of GIS technologies like mobile apps, digital maps, drones, and dashboards, construction leaders can analyze waste-related data geographically and improve their sustainability efforts.
Digital Tools Power On-Site Operational Intelligence
Most construction materials are candidates for a second life: wood chips can be turned into cardboard; gravel and cement are often crushed and repurposed in aggregate concrete; some glass, plastics, and metals can be melted down and formed into new products. With the right kind of operational intelligence, construction companies can spot those second-life opportunities. They can also find ways to cut out excess supplies and shift to reclaimed materials.
Many materials on a construction site need to be carefully separated, but there’s an efficiency payoff to that work because recycling can be more cost-effective than sending material to a landfill. In addition, by tracking and sorting waste, managers can identify which supplies were overpurchased—important for both reusing leftover materials and reducing order sizes at a time when construction supply chains are stressed.
Location-enabled data collection apps make gathering waste-related information and following management protocols less messy. From a phone or tablet, an on-site worker can record details like debris type and volume. Adding photographs reveals whether the waste is in reusable or recyclable condition. Integrated maps help those who move and sort debris identify where the waste is located and where specific materials should be stored on-site.
Additional operational intelligence can be realized using drones, artificial intelligence (AI), and GIS-driven flight planning and imagery analysis. Drones flown over construction and demolition sites can capture critical situational information. Debris can be identified remotely from the images—machine learning algorithms can even scan large batches of images for specific types of waste. Drones are also an asset at dangerous work sites, where they can identify whether debris is salvageable without putting on-the-ground personnel near hazardous material or unstable terrain.
Shared Visibility Drives Next Steps and Portfolio-Wide Improvements
In addition to creating work-site efficiencies, digital data collection puts accurate intelligence in the hands of decision-makers faster. Information captured via app or drone can sync in near real time with a GIS platform, producing a map-based view that guides decisions once waste is identified and sorted.
The operational intelligence delivered by a smart map extends beyond the work site, answering questions like where the closest processing facilities are located or whether nearby jobsites could repurpose excess materials. From the same dashboard, leaders can see up-to-date metrics on a jobsite, find patterns in how waste is generated and disposed of across the company, and create reports for stakeholders or certification boards.
Conversations about sustainable infrastructure often focus on completed projects—energy-efficient high-rises, transit-accessible residential spaces, retail centers that complement the natural landscape. But for the companies bringing these structures to life, sustainability is a process as much as it is an outcome. GIS and companion geospatial technologies provide a smart system for ensuring sustainable practices at every step of the project life cycle. Armed with location-centered operational intelligence, companies can choose greener materials, find new ways to reuse and recycle waste, and use resources more efficiently in their builds.
The Esri Brief
Trending insights from WhereNext and other leading publicationsTrending articles
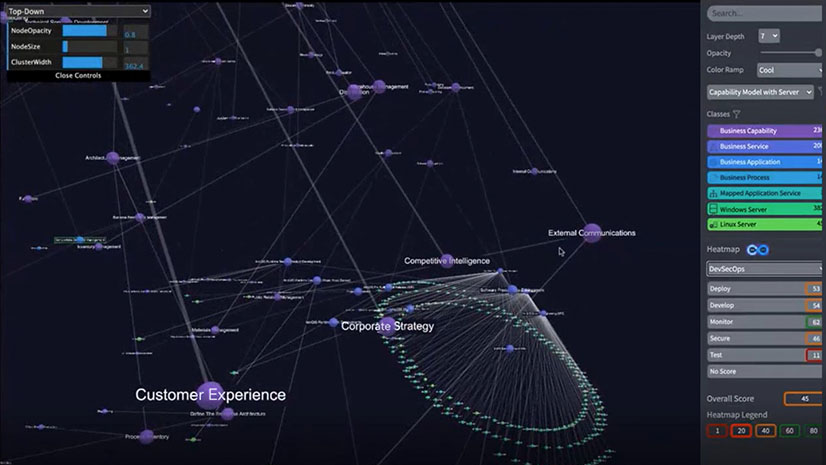
December 5, 2024 |
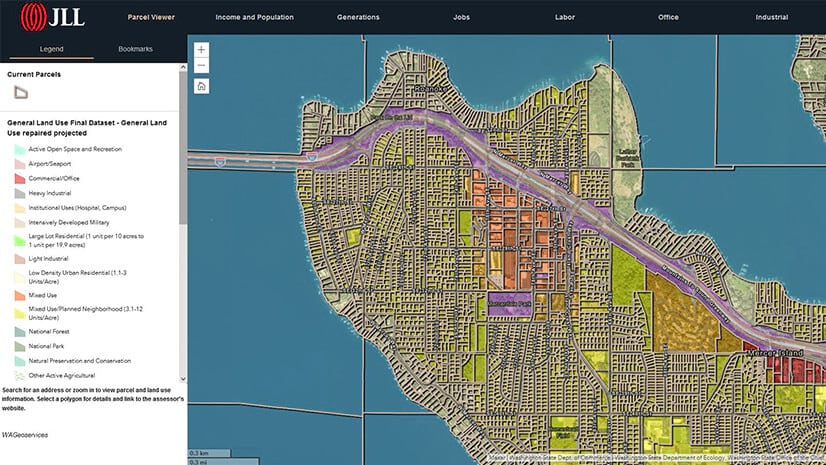
July 25, 2023 |
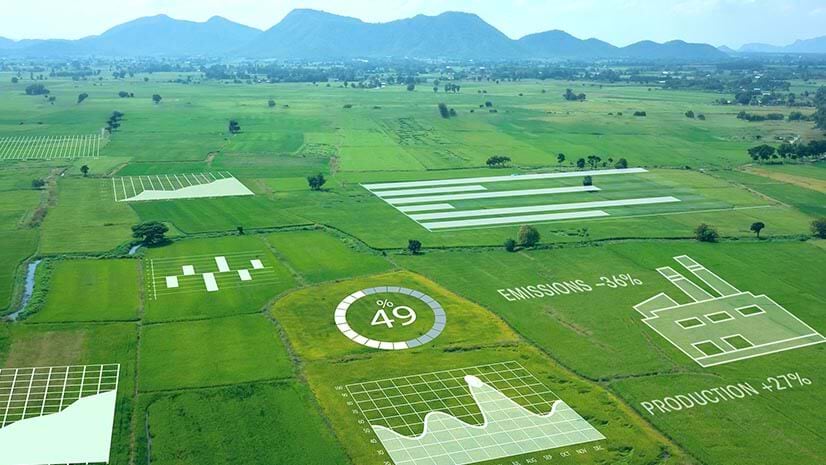
November 25, 2024 |
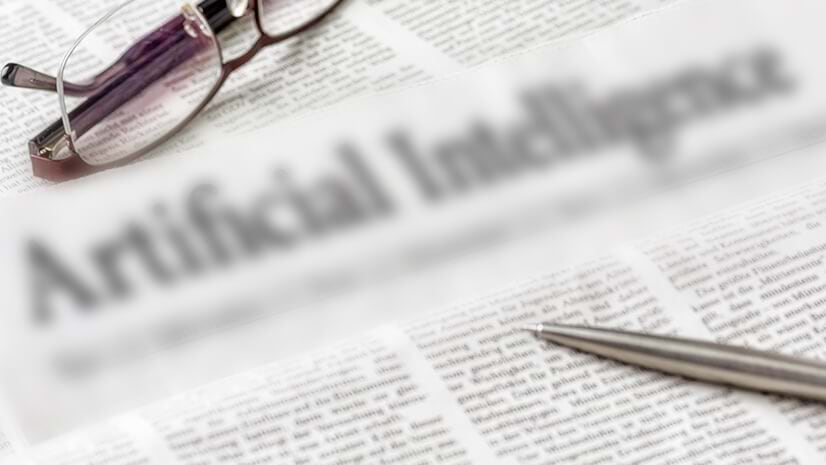
February 25, 2025 |
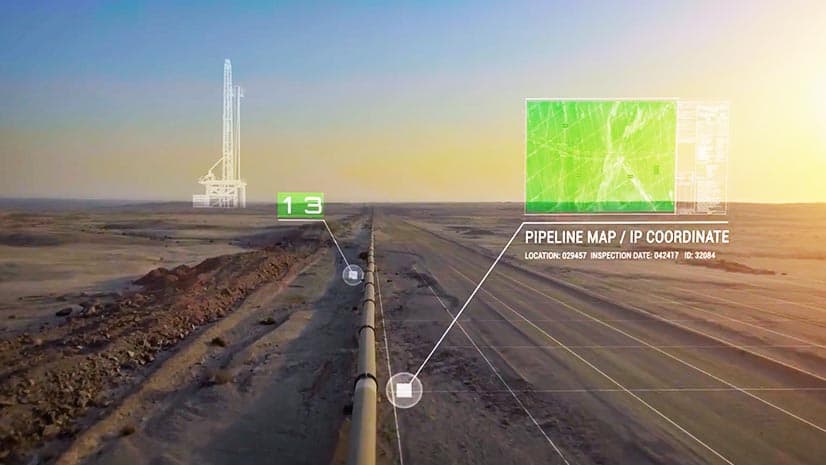
November 12, 2018 |
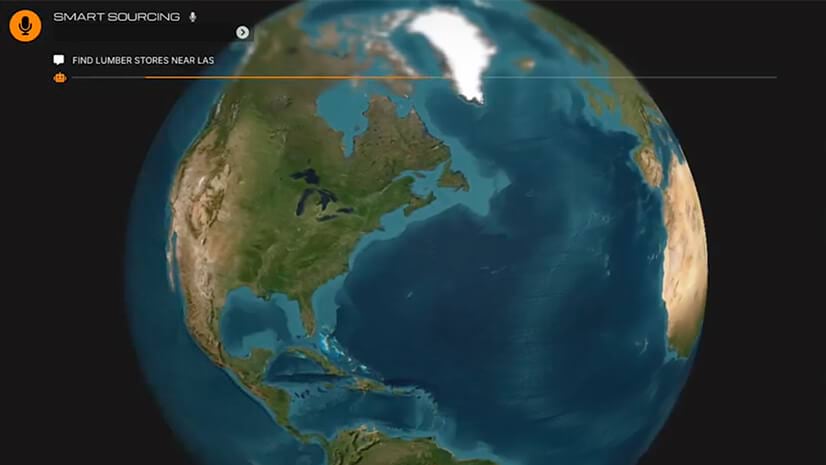
April 1, 2025 |